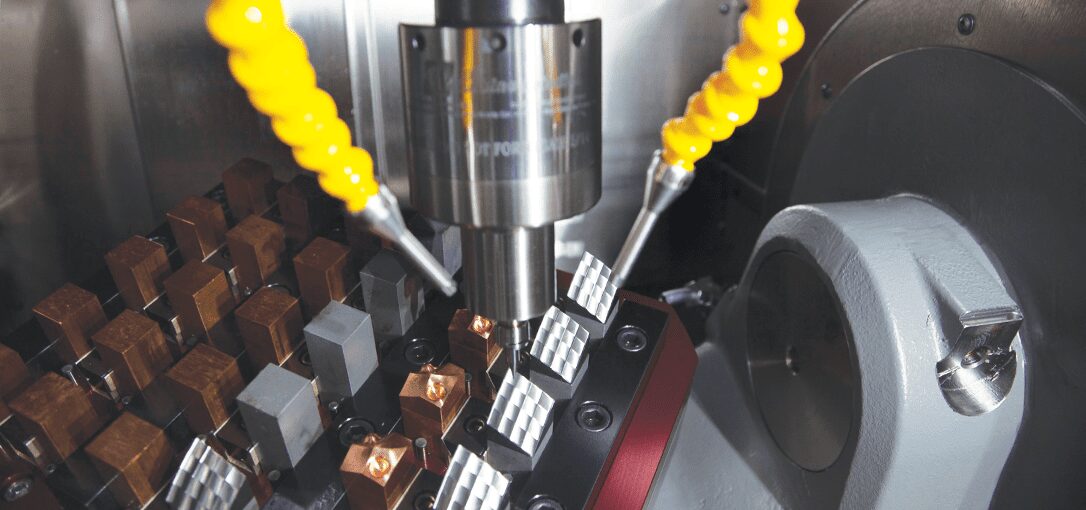
Air Turbine Spindles® vs.
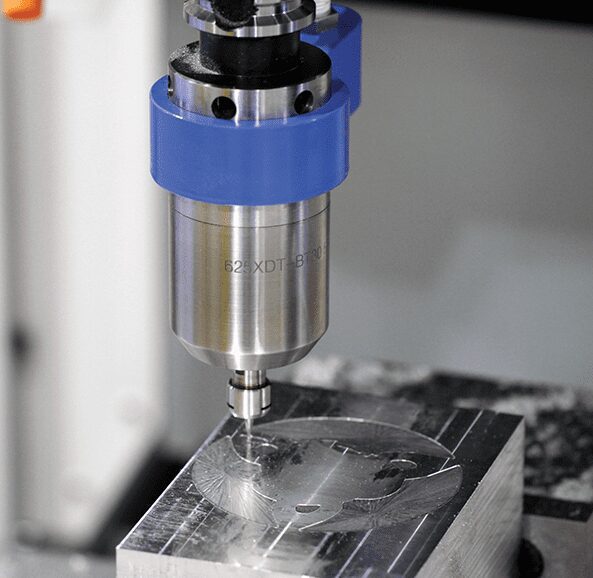
Estimated Speed Range
vs. Specified Constant Speeds
Coolant-driven spindles operate at an estimated speed range described as: “approximate rpm values – depend on pressure, flow rate and used coolant type”. The maximum approximate speed available is 50,000 rpm.
Air Turbine Spindles® rotate within 10% of a specified fixed constant speed of 25,000 to 90,000 RPM determined by the port architecture
Slowing RPM vs.
Governor Controlled High Speed
Coolant-driven spindle specifications state: “The spindle rotates at its rated speed when idle. When the cutting tool enters the workpiece, it is expected that the rotation speed might slow down by several thousand rpm.”
Air Turbine Spindles® is governor-controlled. This means that airflow increases if the rotational speed slows and is maintained at high speed under load when you start cutting – even on angles and hard materials.
No Power Rating
vs. 1.4 hp (1 kW)
Coolant Driven spindles specifications state No Power Rating and state small tools
shouldn’t be used. Coolant spindles have low power.
Air Turbine Spindles® delivers up to 1.4 hp (1 kW) on-demand to maintain high speed on the
toolpath so you can mill 10,000mm/min in HSC 60+ steel with 1/4” / 6 mm tools. High Speed
without a gov.
Filtration and Reduction of Coolant
vs. 90 psi (6.2 bar) Air Supply
Coolant-driven spindles require filtration and a coolant pressure reduction system.
Air Turbine Spindles® are powered by 90 psi / 6.2 bar compressed air and no coolant or reduction
is required. A free filter regulator is included in standard equipment.
Chip Loaded Coolant
vs. Compressed Air
Coolant contains various substances, including chips, which can cause clogging or corrosion in a coolant-driven spindle, or solidify and bacteria grow if static, requiring repairs. Coolant can also leak into your CNC’s spindle causing an expensive repair and downtime.
Air Turbine Spindles® has only compressed air in circulation. These direct drives operate with just 2 moving parts: a powerful proprietary turbine and 2 ceramic grease-packed precision bearings. Air Turbine Spindles® life often exceeds 4,000 hours depending on the application.
Automatic Loading - Coolant only vs. Flexible Options for Air Supply
Coolant-driven spindles require a pressure-reduced filtered supply of coolant and load automatically from the magazine.
Air Turbine Spindles® load automatically and connect to compressed air available at every CNC. Select through spindle air from the machine air blast or our patented Auto-Changer Assembly making set up easy. Manual connection by NPT is also available.
Unknown T.I.R. vs. 2µ Accuracy
Coolant-driven spindles state no T.I.R statistic.
Air Turbine Spindles® certify 2µ precision.
Energy Efficiency - 20 - 40 bar
vs. 6.2 bar (90 psi)
Coolant Driven Spindles use 20 – 40 bar coolant pressure reduced from much higher pressures.
This system is not energy efficient.
Air Turbine Spindles® governor-controlled airflow induces only the exact amount of airflow
needed to drive the tool, resulting in the economical use of compressed air. The result is energy
efficiency. Air Turbine Spindles® uses only 6.2 bar / 90 psi air pressure, not high pressures used with coolant.
Availability of Compressed Air in Every Machine Shop
Coolant Driven Spindles require coolant. Not every CNC user has or needs coolant in his machine or wants coolant in his process. With some materials coolant undesirable.
Air Turbine Spindles® use 90 psi / 6.2 bar available at every machine, clean air cannot contaminate work material and it costs very little.
Observation of Speed Falloff vs. Constant Governed High Speed
Coolant Driven Spindles offer an accessory Digital Tachometer.
Air Turbine Spindles® do not need not this option. A simple tachometer will show the rotational speed remains close to rated speed up to 80%+ of maximum power. View Air Turbine Spindles® at airturbinetools.com
Service & Support
Support is always available from our technical team in the USA and Germany. Repair Service is available in Florida and Munich. Call our factory technicians at +1-561-994-0500 or email us at [email protected].