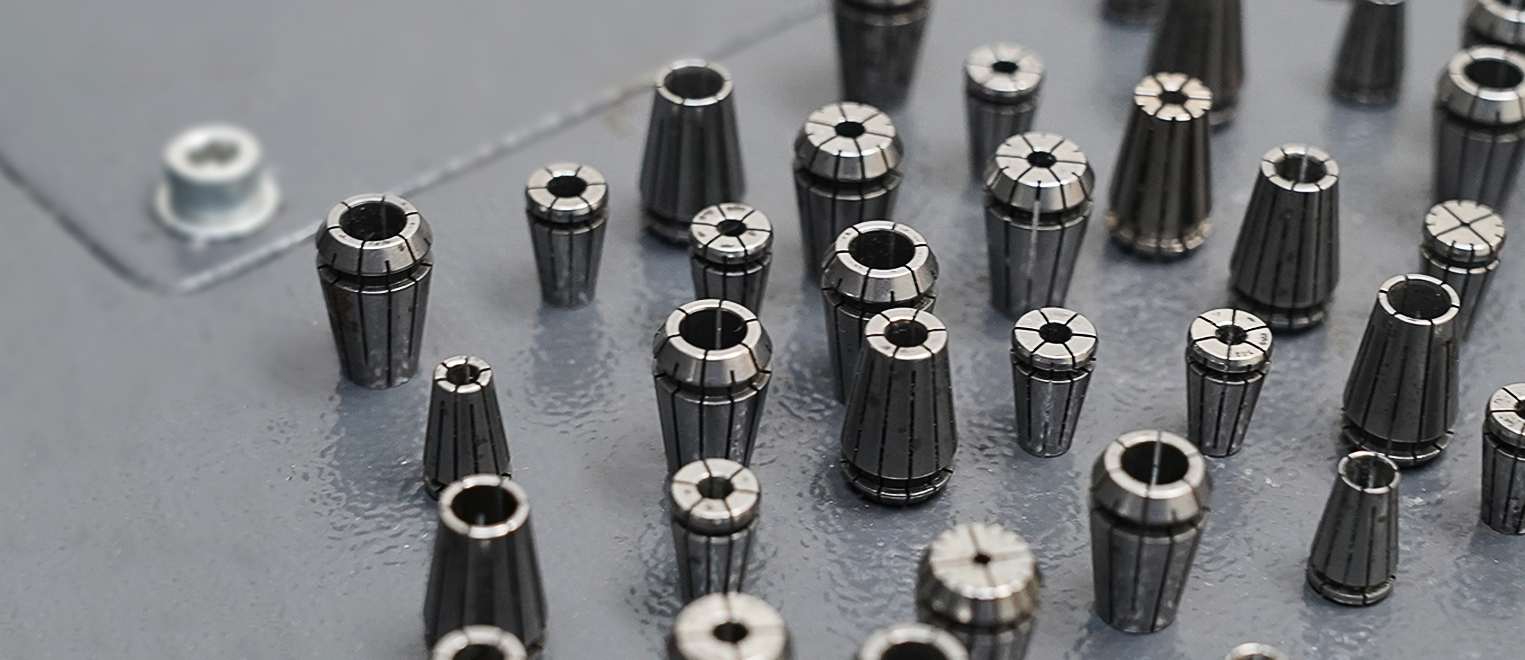
INDEX
►
►
►
►
►
►
CNC Collets: Types and Sizes to Choose From
In the world of high-performance machining, CNC collets are the unsung heroes that seamlessly connect precision with productivity. At Air Turbine Tools®, we understand that these small yet mighty components are pivotal to achieving exceptional results, especially when operating at our ultra-high speeds of 25,000 to 90,000 RPM with 2 micron TIR. Our tools are engineered for excellence, and understanding the role of CNC collets is essential for harnessing full potential.
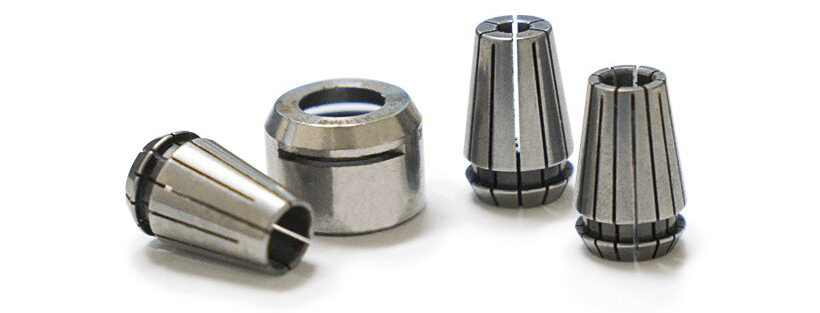
In this guide, we dive deep into the world of CNC collets, examining the wide array of options available to machinists—from DA to TG and ER collets, each designed to meet specific machining demands. Selecting the right collet is a nuanced process, involving critical considerations such as size, runout tolerance, material composition, brand reputation, and clamp force. These factors are crucial in ensuring the high precision and performance that is synonymous with Air Turbine Tools®.
Moreover, regular maintenance of your CNC collets is vital to sustain their longevity and reliability, preventing wear and tear and ensuring they deliver peak performance throughout their lifespan. Should you need assistance or have questions about CNC collets, our dedicated support team is always ready to help, complemented by a detailed FAQ section that addresses common inquiries.
Join us as we explore the intricacies of CNC collets, empowering you to make informed choices that enhance your machining precision and efficiency with Air Turbine Tools'® cutting-edge technology.
CNC Collet Overview
A CNC collet is a clamping device used widely in machining operations to hold onto a workpiece or cutting tool securely. It fits inside a spindle, chuck, or holder of a machine tool, providing a precise and tight grip that prevents the object from moving during the machining process. Unlike traditional clamping methods, CNC collets offer superior accuracy and flexibility by evenly distributing clamping forces around the workpiece or tool. They come in various shapes and sizes, designed to accommodate different diameters and shapes of tools and workpieces. This adaptability makes them indispensable in achieving high-precision machining results, particularly in operations requiring intricate detailing and fine finishes. With their ability to minimize vibration and ensure optimal alignment, CNC collets play a pivotal role in enhancing the overall performance and productivity of CNC machines.
What Are Collets?
Collets are specialized clamping devices designed to hold a workpiece or a tool securely in place during machining operations. They function by forming a collar around the object they are intended to hold, exerting a strong, even pressure when tightened. This ensures that the item is secured firmly, minimizing any movement or slippage which could lead to inaccuracies in the machining process.
How collets work is relatively straightforward yet ingenious. When a collet is inserted into the collet chuck and the nut is tightened, it compresses the collet, causing it to contract onto the tool or workpiece with precise and uniform pressure. This mechanism allows for significant holding strength without damaging the tool or workpiece. Moreover, because they come in various sizes and can accommodate different shapes, collets are highly versatile components of CNC machinery, enabling high-precision outcomes across a wide range of machining tasks.
Add These High Speed Spindles to Your CNC for 5 X Faster Production
What Are Computer Numerical Control (CNC) Machines?
Computer Numerical Control (CNC) machines are automated machining tools that are controlled by a computer program. These programs use numerical data to direct the movement and operation of the machine’s cutting and shaping tools. CNC machines can perform complex cuts with high precision and repeatability, making them invaluable in the manufacturing of metal and plastic parts where accuracy is critical. They have revolutionized modern manufacturing processes, enabling the production of intricate designs that would be difficult or impossible to achieve with manual machining methods. From milling machines and lathes to routers and grinders, CNC technology is utilized in various applications, streamlining production, enhancing efficiency, and reducing human error in industries ranging from aerospace engineering to consumer electronics.
Air Turbine Spindles® and Air Turbine Live Tools® can retrofit any CNC machine with high speed.
Collet Types and Sizes
The versatility and efficiency of CNC machinery are greatly enhanced by the use of collets, a critical component in the precise holding of tools and workpieces. Collets come in various types and sizes, each designed to fulfill specific requirements based on the machine’s application and the nature of the task at hand. This adaptability allows for a wide range of machining operations, from fine engraving to heavy-duty milling. Understanding the differences among collet types and selecting the appropriate size are essential steps in optimizing CNC machine performance, ensuring both accuracy in production and longevity of the equipment.
Double-Angle (DA) Collets
Doubled-Angle (DA) collets, known for their distinctive design which features two separate angles on the taper, are instrumental in precision machining. This unique configuration allows for a more secure grip on the tool, enhancing both accuracy and stability during operations. DA collets come in various sizes, typically identified by numbers such as DA100, DA200, up to DA300, indicating the increasing diameter capacity and overall size of the collet. They are utilized across a broad spectrum of machining tasks but are especially favored for applications requiring high levels of precision and minimal tool slippage, such as drilling and fine milling.
The benefits of using doubled-angle collets are multifaceted. Firstly, their design ensures a uniform force distribution around the tool shank, which significantly reduces the chances of tool deflection and promotes a higher degree of accuracy in machining tasks. Additionally, the improved grip strength minimizes vibration during operation, leading to smoother finishes on machined parts and extending both the tool’s and machine’s lifespan by reducing wear and tear. These features make DA collets an invaluable component in settings that demand precise tolerances and high-quality finishes.
TG Collets
TG collets, known for their versatility and precision, are a type of machine tool accessory used to hold workpieces or cutting tools. Characterized by their unique tapered shape, TG collets provide excellent clamping force and accuracy. They come in a variety of sizes, typically ranging from small diameters suitable for delicate machining tasks to larger ones capable of accommodating substantial workpieces. This size range makes TG collets adaptable for use in a wide array of machining operations, from fine detailed work to heavy-duty cutting.
One of the primary benefits of TG collets lies in their ability to maintain a consistent grip on the tool or workpiece, significantly reducing slippage and increasing machining accuracy. Their design also minimizes vibration during operation, which not only improves the quality of the finish but also extends the lifespan of both the machine tool and the collet itself. Furthermore, TG collets offer easy setup and changeover, saving valuable time in high-production environments. These characteristics make TG collets an essential component for manufacturers seeking efficiency without compromising on precision or quality.
ER Collets
ER collets are a versatile and widely used type of tool holding system, designed to accommodate a wide range of tool diameters within a single collet. They come in various sizes, labeled as ER11, ER16, ER20, ER25, ER32, ER40, and so forth, indicating the maximum diameter of the tool shank that can be accommodated. The size ranges typically from very small diameters up to 26 mm or about1 inch. This flexibility makes them ideal for different machining applications including milling, drilling, and tapping across various industries.
One of the main benefits of ER collets is their exceptional clamping force and accuracy. They securely hold tools in place even at high speeds or under heavy torque conditions. Moreover, ER collets have a unique self-releasing mechanism that enhances safety and convenience during tool changes. The wide clamping range also means fewer collets are required to cover a range of tool sizes, which reduces inventory costs and simplifies setup processes. Additionally, the standardized design ensures compatibility with various machines and spindles, making them an efficient and adaptable option for manufacturers aiming for precision and reliability in their operations.
Factors to Consider When Choosing a CNC Collet
Before diving into the specifics of collet selection for CNC machines, it’s crucial to note that choosing the right type of collet is not a one-size-fits-all scenario. Several factors come into play, each impacting your machining process’s efficiency, accuracy, and overall success. In the following sections, we will explore these critical considerations in detail to guide you through making an informed decision tailored to your specific needs. From understanding the material compatibility and gripping strength required for your applications to considering ease of maintenance and cost-effectiveness, this guide will cover essential aspects such as size range, compatibility with existing machinery, precision levels, and durability among others. Keep these factors in mind as we delve deeper into what makes a collet stand out as the right choice for your collet CNC operations.
Size
Collets come in a variety of sizes to fit different types of CNC machinery and workpieces. The size of a collet is determined by its inner diameter, which must match the outer diameter of the tool or workpiece it is holding. Choosing the right size collet for your application is crucial as it ensures proper grip and stability during machining.
One important aspect to consider when selecting a collet size is the range of sizes that are compatible with your current machinery. Some collets may have a narrower or wider range than others, so it’s essential to check the specifications and choose one that will work seamlessly with your equipment. Additionally, you should also consider the size range of the tools and workpieces you commonly use in your operations.
Reputation
The reputation of a brand is crucial when selecting a CNC collet, offering not just quality assurance and reliability. Air Turbine Tools® have Rego Fix ultra-precision and PG collets due to the trust in the quality products they produce, innovation and consistent high-performance toolholding solutions. With a legacy of pioneering technology, Rego-Fix provides secure and accurate collet systems.
Choosing a reputable brand like Rego-Fix also grants access to support and service networks, enhancing user experience and satisfaction. Their commitment to excellence ensures consistent quality and performance, allowing manufacturers to optimize machining processes confidently. By selecting brands that epitomize innovation and quality, manufacturers can significantly impact the success of their operations, making brand reputation a vital factor in CNC collet selection.
Runout
Runout is a critical factor to consider when choosing a CNC collet because it directly affects the accuracy and quality of the machining process. Runout refers to the amount of wobble that occurs when a tool spins in its collet, measured as the difference between the tool’s highest and lowest points during rotation. High runout can lead to uneven cutting, reduced tool life, and poor surface finish on the workpiece. Therefore, selecting a collet with minimal runout ensures that the tool remains centered and stable throughout operation, resulting in precise and consistent machining.
Moreover, different types of CNC collets are designed to offer varying degrees of runout tolerance, depending on their manufacturing quality and intended use. For high-precision tasks requiring utmost accuracy, investing in premium quality collets with low runout is indispensable. These collets might come at a higher initial cost but can significantly reduce waste and rework by enhancing overall machining performance. On the other hand, for less critical applications where slight variations are acceptable, standard collets may suffice. Thus, understanding the specific requirements of your machining tasks and how runout impacts them is key to selecting the most appropriate CNC collet for your needs.
Material
When selecting a CNC collet, the material is a crucial factor because it directly affects the collet’s durability, flexibility, and suitability for different machining tasks. Collets are typically made from hard-wearing materials like high-grade tool steel to ensure longevity and precision during use. For instance, spring steel is commonly used for its ability to expand and contract due to its inherent flexibility, making it ideal for spring machine collets in CNC machining.
Other materials like steel offer greater strength and durability but come at a higher cost and weight. Aluminum, while lighter and more affordable, lacks the strength of steel, making it suitable for applications where reduced weight is more critical than maximum durability. Brass and nylon are also used for specialized collets, like expanding and emergency collets, offering unique properties such as ease of machining and specific expansion capabilities. Therefore, the choice of material depends on the specific requirements of the machining operation, including the need for flexibility, strength, weight, and cost considerations.
Clamp Force
Clamp force is a critical factor in the selection of CNC collets due to its direct impact on machining accuracy and tool life. A collet with appropriate clamp force ensures that the cutting tool is securely held in place during the machining process, preventing slippage and potential damage to both the tool and the workpiece. This is especially important during high-speed operations or when working with hard materials, where the forces exerted on the tool are significantly greater. The right clamp force not only enhances precision but also supports optimal cutting conditions, thereby extending tool life and improving overall productivity.
Moreover, insufficient or excessive clamp force can lead to various machining issues. Too little force may result in tool displacement or ejection under load, leading to inaccuracies, poor finish quality, and increased risk of accidents. Conversely, excessive clamping can cause deformation of the tool shank, impairing its balance and concentricity which adversely affects machining precision and could accelerate wear. Therefore, selecting a CNC collet that provides an ideal balance of clamp force is essential for maintaining high standards of safety, efficiency, and workpiece quality throughout manufacturing processes.
CNC Collet Installation
Proper installation of a CNC collet is crucial for achieving optimal performance and maintaining the integrity of your tooling and workpieces. Here’s a step-by-step guide to ensure correct setup, inspired by best practices:
►
►
►
►
►
►
►
Remember, taking time to install your CNC collets correctly can save you time and resources by preventing machining errors and extending tool life. Always refer back to specific product manuals or guides like those provided at Air Turbine Tools® for detailed instructions tailored to your equipment.
CNC Collet Maintenance Tips
When it comes to maintaining your CNC collets, a few key tips can ensure their longevity and optimal performance. Regular inspection for wear and tear is crucial, as even minor damage can affect machining accuracy. Cleaning the collets and the collet cavity in the spindle helps prevent the buildup of debris keeping your collets in top condition.
Maintain Routine Cleanings:
To maintain your CNC collets effectively, it’s essential to perform routine cleanings after each use. This involves removing any chips, coolant, or oil residue from both the collet and its cavity to ensure a debris-free environment that promotes precision and longevity.
Replace Collets When Needed:
It is important to replace your CNC collets when needed, as worn or damaged collets can significantly impact the precision and longevity of your machine. Regular inspections will help identify when replacements are necessary, ensuring continued high-quality performance.
Conduct Inspections:
Regular inspections of your CNC collets are critical to ensuring optimal performance. Make sure to conduct these inspections by following proper procedures and using appropriate tools and equipment. This will help identify any wear or damage early on, allowing for timely repairs or replacements before major issues arise.
Etc.:
Additionally, be sure to properly store and handle your collets to avoid any unnecessary damage. Utilizing proper storage methods, such as using a collet holder, can also help extend the lifespan of your collets.
Contact Us Today With Your Installation Questions
CNC collets are essential for precision machining, providing a secure grip on workpieces or cutting tools and enhancing productivity. They fit inside a machine tool’s spindle to ensure accurate and stable machining by evenly distributing clamping forces.
This guide explored the different types of collets—DA, TG, and ER—and offered insights on choosing the right one for your application.
When selecting a CNC collet, consider:
Proper Installation and Maintenance are Essential
For installation, follow our collet installation guide. Regular cleaning, safe inspections, and timely replacements help maintain collet performance and life.
Air Turbine Tools® stands ready to assist. With a commitment to high speed machining, Air Turbine Tools® can help clarify any installation queries you may have or explore more about what sets them apart in the industry—the ATT Difference. Do not hesitate to reach out for guidance on reducing your cycle times 6x-10x and improving your production.
FAQs
What is the purpose of a collet?
A collet is a clamping device used to hold a workpiece or tool in place. It exerts a strong clamping force on the item being held, providing precision and stability during machining processes.
What is the purpose of a collet?
The purpose of a collet is to securely hold a workpiece or tool in place during machining operations. It ensures precision and stability by applying a uniform clamping force around the object.
How long do CNC collets last?
The lifespan of CNC collets can vary widely based on usage, material quality, and maintenance practices. Typically, with proper care and under normal working conditions, a CNC collet can last anywhere from 3 to 7 years. Regular inspection and cleaning are crucial to maximize their lifespan.
What are the signs it’s time to replace a CNC collet?
Signs it’s time to replace a CNC collet include noticeable wear or damage, decreased precision in machining operations, difficulty in securing tools or workpieces, and an increase in vibration during use. If the collet does not release the tool or workpiece smoothly or if there are visible cracks, it is definitely time for a replacement.
What is the correct method to assemble a collet and collet nut?
The correct method to assemble a collet and collet nut involves several steps to ensure proper function and safety. Start by inspecting both the collet and the collet nut for any damage or debris. Clean them if necessary. Insert the collet into the collet nut, making sure it snaps into place securely. Then, thread the collet nut onto the machine’s spindle or tool holder without a tool inserted. Only after the collet nut is loosely fitted should you insert the tool into the collet. Finally, tighten the collet nut according to the manufacturer’s recommended torque settings to secure the tool in place.
Service & Support
Support is always available from our technical team in the USA and Germany. Repair Service is available in Florida and Munich. Call our factory technicians at +1-561-994-0500 or email us at [email protected].