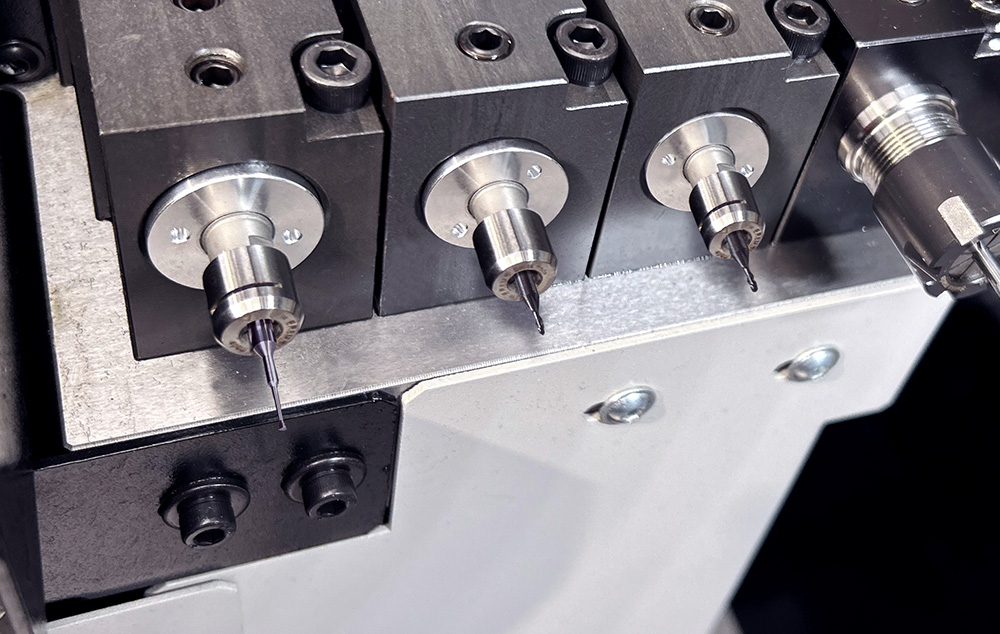
- Home
- Products
- Air Turbine Live Tools®
- User Notes
INDEX
►
►
►
►
►
►
►
►
►
Read all instructions thoroughly before installation and use.
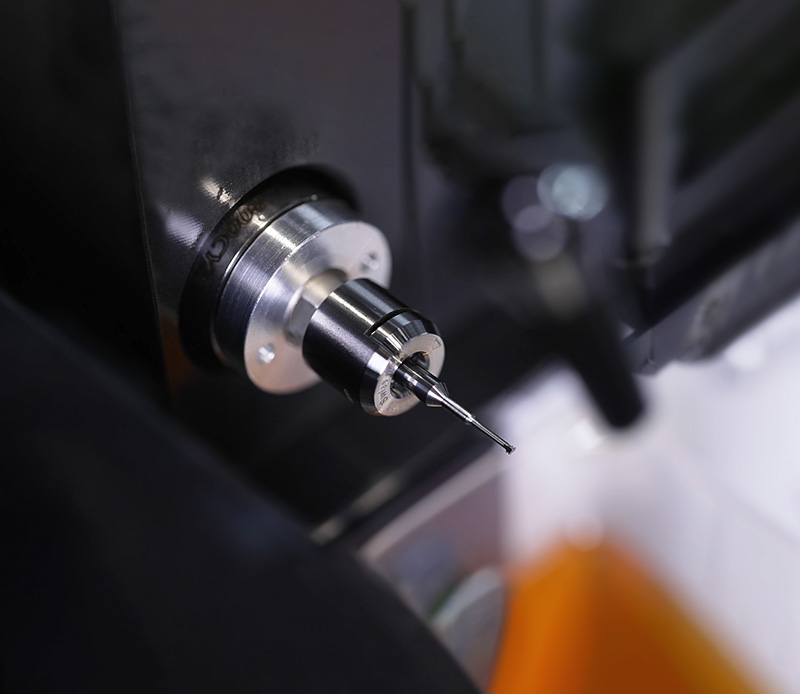
Downloadable PDF Content
User Notes and Setup
Accessory Part Numbers
Initial Installation
Install a new dedicated clean air line from a filter/regulator to your Air Turbine Live Tool® as shown in the diagram below. Filter/regulators are included with the Air Turbine Live Tools® and are available for an additional purchase.
Ensure all air lines and fittings meet the minimum internal diameter specified for your model as specified in figure 2. Additionally, place a plug in any air inlet that is not being used.
Install exhaust hoses as shown in figure 1. Internal diameters of exhaust hoses must be no smaller than the specified minimum required ID for your model, as shown in figure 2.
Connection to air supply starts live tool rotation. Do not connect air to your tool until installation is complete.
Optional: If you have a manual shut-off valve, install it after the filter/regulator. Using a manual valve is recommended.
Figure 1: A clean airline from a filter/regulator to a mounted Air Turbine Live Tool® with exhaust hoses installed.
Air Hoses and Fittings Requirements
Avoid fittings, couplings and hoses with a smaller internal diameter than the minimum required for your model. Any connections smaller than the minimum will restrict air flow and reduce power to your Air Turbine Live Tool®. You can find the minimum required internal diameter (ID) for fittings and hoses for your tool on the table shown in figure 2 below.
Air flow restrictions (such as air leaks and obstructions) will cause underpower performance and drag your tool through the material, damaging the bearings. Some fittings with nominal internal dimensions may have an ID passage that is smaller than stated and restrict air flow and power. It only takes one fitting with an internal diameter that is too small to reduce air flow and power of your Air Turbine Live Tool®.
Air Hoses and Fittings Requirements for Air Turbine Live Tools® | ||
Model | Hose/Connector Minimum Required Internal Diameter | |
Metric | Imperial | |
| 4 mm | 5/32” |
| 5 mm | 0.1969” |
| 6 mm | 15/64” |
Air Hoses, Connections, Fittings Minimumn Internal Diameter Requirements for Air Turbine Live Tools® |
Model |
|
|
|
Hose/Connector Minimum Required Internal Diameter | |
Metric | Imperial |
4 mm | 5/32” |
5 mm | 0.1969” |
6 mm | 15/64” |
Figure 2: Air Turbine Live Tools® hose/fitting/connector internal diameter specifications.
Air Requirements
Ensure there is sufficient volume of clean compressed air flow at 90 psi/6.2 bar with the specified air flow volume CFM (L/s) for your model as shown in figure 3 to maintain working air consumption. Depending on application, consider peak or stall capacity consumption. Our governor increases air flow volume on demand to keep rotation at the high speed when your tool starts to cut. Air pressure and flow volume must therefore be available on demand and remain constant with no drop over time or when cutting.
Refer to figure 3 for the idle CFM (L/s) rating vs. working air consumption ratings for all models of Air Turbine Live Tools®.
Connection to air supply starts live tool rotation. Do not connect air to your tool until installation is complete.
Do not oil or lubricate. Use dry, clean, oil free 90 psi (6.2 bar) air supply only.
Avoid pressure below 90 psi (6.2 bar), which causes the tool to be dragged through the material, causing rapid bearing wear and underpowered performance. Do not use more than 100 psi (6.9 bar) pressure which will burst the turbine power producer.
Air pressure and flow must remain constant with no drops under cutting load. Insufficient flow will cause the rotation of your tool to slow or stop suddenly, damaging the bearings. If a drop in psi (bar) occurs below 90 psi (6.2 bar), your compressor may not have enough CFM (L/s) to power the Air Turbine Live Tool® or there is a flow restriction in the air line.
Idle CFM/L/s Rating vs. Working Air Consumption Ratings
Air Turbine Live Tools® consume more air as the cutting load or the amount of material removed increases.
This is normal operation of our patented governor which maintains high speed on your tool path and makes Air Turbine Live Tools® efficient in air consumption.
Air Turbine Live Tools® Idle and Working Air Consumption Ratings |
|||
Model | Speed | Air Consumption Idle | Air Consumption Working Flow |
| 60,000 RPM | 3.5 CFM (1.65 L/s) | 5 CFM (2.36 L/s) |
80,000 RPM | |||
| 50,000 RPM | 4 CFM (1.89 L/s) | 6 CFM - 9 CFM (2.83 L/s - 4.24 L/s) |
65,000 RPM | |||
| 40,000 RPM | 5 CFM (2.36 L/s) | 7 CFM - 10 CFM (3.3 L/s - 4.72 L/s) |
50,000 RPM | 6 CFM (2.83 L/s) |
Air Turbine Live Tools® Idle and Working Air Consumption Ratings |
Model |
|
|
|
Speed | Air Consumption Idle | Air Consumption Working Flow |
60,000 RPM | 3.5 CFM (1.65 L/s) | 5 CFM (2.36 L/s) |
80,000 RPM | ||
50,000 RPM | 4 CFM (1.89 L/s) | 6 CFM - 9 CFM (2.83 L/s - 4.24 L/s) |
65,000 RPM | ||
40,000 RPM | 5 CFM (2.36 L/s) | 7 CFM (3.3 L/s) - 10 CFM (4.72 L/s) |
50,000 RPM | 6 CFM (2.83 L/s) |
Figure 3: Idle CFM (L/s) and working air consumption ratings for Air Turbine Live Tools®.
Maintenance
Your Air Turbine Live Tool® must be run at least 10 minutes every 30 days from manufacture date to maintain optimal performance. Run at least 10 minutes before initial use.
The airline must be impeccably clean with no coupling or hose smaller than the minimum internal diameter required for your model as described in figure 2 so that air flow volume is unrestricted.
Purge the airline of contamination before each use.
When installing your cutting tool and collet, never hit the collet nut with the wrench.
A 0.3 micron filter extractor regulator combination is a necessary accessory for Air Turbine Live Tools® to eliminate impurities in your air supply.
Contamination will damage your turbine components and require repair. Filters are included with Air Turbine Live Tools® and are required for all Air Turbine Live Tool® models.
Filter elements need to be changed periodically and extractor drained in regular maintenance cycles.
Mounting Air Turbine Live Tools® into your Lathe
It is important that your fixture is not clamped over the bearings. Incorrect positioning or over tightening of the clamp on your Air Turbine Live Tool’s® steel barrel results in pressure on the bearings, causing premature failure. To avoid this error in installation, refer to the dimensions of your model in figure 4 or on your models specification sheet.
822CX Dimensional Drawing
822CX Dimensions | |||||
A | Ø 0.47" (12 mm) | C | 3.09" (78.36 mm) | E | Ø 0.86”(22 mm) |
B | 0.72” (18.29 mm) | D | 2.9” (73.53 mm) |
822CX Dimensions | |
A | Ø 0.47" (12 mm) |
B | 0.72” (18.29 mm) |
C | 3.09" (78.36 mm) |
D | 2.9” (73.53 mm) |
E | Ø 0.86”(22 mm) |
825CX Dimensional Drawing
825CX Dimensions | |||||
A | Ø 0.47" (12 mm) | C | 3.09" (78.36 mm) | E | Ø 0.98”(25 mm) |
B | 0.72” (18.29 mm) | D | 2.9” (73.53 mm) |
825CX Dimensions | |
A | Ø 0.47" (12 mm) |
B | 0.72” (18.29 mm) |
C | 3.09" (78.36 mm) |
D | 2.9” (73.53 mm) |
E | Ø 0.98”(25 mm) |
820MX Dimensional Drawing
820MX Dimensions | |||
A | 0.65" (16.51 mm) | D | 1.99" (50.55 mm) |
B | Ø 0.79" (20 mm) | E | Ø 1.18 (30 mm) |
C | 2.03" (51.56 mm) | F | 4.99" (126.75 mm) |
820MX Dimensions | |
A | 0.65" (16.51 mm) |
B | Ø 0.79" (20 mm) |
C | 2.03" (51.56 mm) |
D | 1.99" (50.55 mm) |
E | Ø 1.18 (30 mm) |
F | 4.99" (126.75 mm) |
822MX Dimensional Drawing
822MX Dimensions | |||
A | 0.65" (16.51 mm) | D | 1.99" (50.55 mm) |
B | Ø 0.85" (21.6 mm) | E | Ø 1.18 (30 mm) |
C | 2.03" (51.56 mm) | F | 4.99" (126.75 mm) |
822MX Dimensions | |
A | 0.65" (16.51 mm) |
B | Ø 0.85" (21.6 mm) |
C | 2.03" (51.56 mm) |
D | 1.99" (50.55 mm) |
E | Ø 1.18 (30 mm) |
F | 4.99" (126.75 mm) |
825MX Dimensional Drawing
825MX Dimensions | |||
A | 1.09” (27.61 mm) | D | 0.5" (12.7 mm) |
B | Ø 1.0” (25.40 mm) | E | Ø 1.57" (40 mm) |
C | 1.5" (38.1 mm) | F | 4.0" (101.6 mm) |
825MX Dimensions | |
A | 1.09” (27.61 mm) |
B | Ø 1.0” (25.40 mm) |
C | 1.5" (38.1 mm) |
D | 0.5" (12.7 mm) |
E | Ø 1.57" (40 mm) |
F | 4.0" (101.6 mm) |
800LT Dimensional Drawing
Ø 19.05 mm OD
800LT 19.05 mm OD Dimensions | |||||
A | Ø 0.47" (12 mm) | E | 1.0” (25.4 mm) | I | Ø 0.17" (4.32 mm) THRU Ø 0.29" (7.4 mm) ↧ 0.16" (4.06 mm) TYP (2) |
B | 0.57" (14.47 mm) | F | Ø 0.75″ (19.05 mm) | ||
C | 1.56" (39.62 mm) | G | 0.51″ (12.95 mm) TYP (2) | ||
D | 3.34″ (84.84 mm) | H | 0.30" (7.62 mm) TYP (2) |
800LT 19.05 mm OD Dimensions | |
A | Ø 0.47" (12 mm) |
B | 0.57" (14.47 mm) |
C | 1.56" (39.62 mm) |
D | 3.34″ (84.84 mm) |
E | 1.0″ (25.4 mm) |
F | Ø 0.75″ (19.05 mm) |
G | 0.51″ (12.95 mm) TYP (2) |
H | 0.30" (7.62 mm) TYP (2) |
I | Ø 0.17" (4.32 mm) THRU Ø 0.29" (7.4 mm) ↧ 0.16" (4.06 mm) TYP (2) |
800LT Dimensional Drawing
Ø 20 mm OD
800LT 20 mm OD Dimensions | |||||
A | Ø 0.47" (12 mm) | E | 1.0″ (25.4 mm) | I | Ø 0.17" (4.32 mm) THRU Ø 0.29" (7.4 mm) ↧ 0.16" (4.06 mm) TYP (2) |
B | 0.57" (14.47 mm) | F | Ø 0.79″ (20 mm) | ||
C | 1.56" (39.62 mm) | G | 0.51″ (12.95 mm) TYP (2) | ||
D | 3.34″ (84.84 mm) | H | 0.30" (7.62 mm) TYP (2) |
800LT 20 mm OD Dimensions | |
A | Ø 0.47" (12 mm) |
B | 0.57" (14.47 mm) |
C | 1.56" (39.62 mm) |
D | 3.34″ (84.84 mm) |
E | 1.0″ (25.4 mm) |
F | Ø 0.79″ (20 mm) |
G | 0.51″ (12.95 mm) TYP (2) |
H | 0.30" (7.62 mm) TYP (2) |
I | Ø 0.17" (4.32 mm) THRU Ø 0.29" (7.4 mm) ↧ 0.16" (4.06 mm) TYP (2) |
800LT Dimensional Drawing
Ø 22 mm OD
800LT 22 mm OD Dimensions | |||||
A | Ø 0.47" (12 mm) | E | 1.0″ (25.4 mm) | I | Ø 0.22" (5.58 mm) THRU Ø 0.32" (8.13 mm) ↧ 0.3" (7.62 mm) TYP (2) |
B | 0.57" (14.5 mm) | F | Ø 0.87″ (22 mm) | ||
C | 1.56" (39.62 mm) | G | 0.74″ (18.8 mm) TYP (2) | ||
D | 3.34″ (84.84 mm) | H | 0.27" (6.86 mm) TYP (2) |
800LT 22 mm OD Dimensions | |
A | Ø 0.47" (12 mm) |
B | 0.57" (14.5 mm) |
C | 1.56" (39.62 mm) |
D | 3.34″ (84.84 mm) |
E | 1.0″ (25.4 mm) |
F | Ø 0.87″ (22 mm) |
G | 0.74″ (18.8 mm) TYP (2) |
H | 0.27" (6.86 mm) TYP (2) |
I | Ø 0.22" (5.58 mm) THRU Ø 0.32" (8.13 mm) ↧ 0.3" (7.62 mm) TYP (2) |
800LT Dimensional Drawing
Ø 25 mm OD
800LT 25 mm OD Dimensions | |||||
A | Ø 0.47" (12 mm) | E | 1.0″ (25.4 mm) | I | Ø 0.17" (4.32 mm) THRU Ø 0.32" (8.13 mm) ↧ 0.46" (11.68 mm) TYP (2) |
B | 0.57" (14.5 mm) | F | Ø 0.97″ (24.89 mm) | ||
C | 1.56" (39.62 mm) | G | 0.65″ (16.51 mm) TYP (2) | ||
D | 3.34″ (84.84 mm) | H | 0.45" (11.43 mm) TYP (2) |
800LT 25 mm OD Dimensions | |
A | Ø 0.47" (12 mm) |
B | 0.57" (14.5 mm) |
C | 1.56" (39.62 mm) |
D | 3.34″ (84.84 mm) |
E | 1.0″ (25.4 mm) |
F | Ø 0.97″ (24.89 mm) |
G | 0.65″ (16.51 mm) TYP (2) |
H | 0.45" (11.43 mm) TYP (2) |
I | Ø 0.17" (4.32 mm) THRU Ø 0.32" (8.13 mm) ↧ 0.46" (11.68 mm) TYP (2) |
822CX
825CX
820MX
822MX
825MX
800LT
Figure 4: Tables that show the proper mounting area and dimensions for mounting all Air Turbine Live Tools®.
Calculating Your New Feed Rate and Cycle Time
You do not need to change the set RPM in your program to operate Air Turbine Live Tools® in your lathe. Instead, change the feed rate in your program.
All Air Turbine Live Tools® operate at a constant factory-set fixed speed, and are tested and rated to be within 10% of the designated speed. The formula in figure 5 below is an approximation for calculating what your new feed rate and cycle time should be. Always consult with an Air Turbine technician for your specific application.
Calculation Variables | |
Variable | Example Value |
Standard Live Tool RPM | 6,000 RPM |
Standard Live Tool Feed Rate | 0.001 IPR |
Standard Live Tool Cycle Time | 60 Minutes |
Air Turbine Live Tool® RPM | 60,000 RPM |
Divide your Air Turbine Live Tool® RPM by the RPM of your main spindle to determine how many times faster the RPM is.
Calculate your new feed rate when using your Air Turbine Live Tool® by multiplying your current feed rate by how many times faster the RPM is.
Calculate your new cycle time by dividing your current cycle time by how many times faster the RPM is.
Figure 5: A set of formulas used to determine your approximate new feed rate and cycle time with an Air Turbine Live Tool® using your main spindles RPM, your current feed rate, and current cycle time.
Operation
Purge the line of contamination and run at least 10 minutes before initial use to ensure the bearing lubrication does not solidify.
Always monitor the air pressure gauge during operation of your Air Turbine Live Tool®. The key to successful high-speed machining and optimized tool performance is to program light passes at very high feed rates. Start with a light pass observing surface finish quality and gradually step down or increase your rate of advance for optimal cutting conditions. Do not try to cut too aggressively. You will overload your turbine causing your cutting tool to stall or drag in the material. Dragging your tool on the work or a sudden stop will cause stress to the bearings and force the grease out, causing premature failure.
Working in a Wet Environment
Air Turbine Live Tools® are sealed for wet environments. In a wet environment, turn on the air supply to your Air Turbine Live Tool® before you turn on the coolant flow. At the end of the cycle turn the coolant off first. Only after the coolant flow is off, then you can turn off the air flow to your tool.
Learn More About Air Turbine Live Tools®
Service & Support
Support is always available from our technical team in the USA and Germany. Repair Service is available in Florida and Munich. Call our factory technicians at +1-561-994-0500 or email us at [email protected].